Nanoscale materials may soon revolutionize energy storage
There’s a cliché about holding the future in the palm of your hand. But if you go to Lowe’s or Home Depot, you might be able to do it. In the power tool aisle, pick up a cordless drill or saw from DeWalt and there might well be a futuristic battery pack attached for long lasting energy storage — a battery that promises greater power, longer life, better safety, and shorter recharge time than conventional batteries.
The battery itself looks little different to the naked eye, or even under a microscope. The key to the battery’s performance is in the diameter of the lithium particles that hold and release electric charge. The so-called nanophosphate lithium ion batteries, developed and manufactured by A123 Systems, based in Watertown, Mass., have particles in their electrolyte—the chemical bridge between the two electrodes of a battery—as small as 100 nanometers, smaller by a factor of hundreds than those found in conventional lithium-ion batteries.
While cordless power tools may be the first application for nanotechnology-based energy storage systems, they certainly won’t be the last. Teams of researchers working around the globe are finding that as the materials in batteries and capacitors become more finely engineered, they increase their energy storage capabilities. Within a decade, nanomaterial-based batteries and capacitors could find themselves not just in power tools and cell phones, but in uninterruptible power supplies, electric vehicles, and even the electric grid, to help handle the wind and solar energy.
The explosion in handheld devices has transformed the sleepy world of energy storage over the past decade. Although alkaline batteries may have been dominant for more than a generation, and lead-acid cells date back to the 1850s, new technologies have been reaching the marketplace at an ever-quickening pace. Rechargeable batteries based on nickel-metal hydride and lithium-ion chemistries have been widely available in the past decade, and are now found in such high-profile applications as laptop computers and hybrid-electric vehicles.

How to store energy efficiently?
Because batteries are playing such a prominent role, researchers are working hard to improve them, eliminating such headaches as recharge memory and packing more energy into each cubic inch. One of the keys to increasing energy density, it turns out, is relying on nanoscale materials. As the particle size is reduced, the surface area of a given mass of material increases; this could enable, say, more reaction area between particles and fluid. Some experts suggest that carbon nanotubes might one day be able to store energy in the form of hydrogen packed within their crevices.
One of the first of the next generation of energy storage technologies to reach the market is A123’s M1 nano-phosphate battery. From the outside, there’s little to distinguish the battery as a product of nanotechnology research.
“The materials we use are smaller than 100 nanometers,” said Ric Fulop, vice president of business development. “It’s a whole new class of material that eliminates some of the problems of conventional lithium-ion systems.” The effect of stray oxygen atoms within the electrolyte, which has been implicated in some safety problems in conventional lithium-ion batteries, is significantly reduced with the nanoscale materials.
“When you go nano,” Fulop said, “you get much faster kinetics. The power of a battery is directly correlated to the diffusion of ions going in and out of the active material. When you pull power from a battery, ions and electrons have to exit or enter the particles that store the energy.” By improving the conductivity of the material to both ions and electrons, the engineers at A123 have developed a battery that can both release a large amount of electricity quickly and recharge in a fraction of the time needed for standard rechargeable batteries.
Manufacturing these batteries requires a new process, Fulop said. “You need a new type of technology to mix the materials, to coat the materials, and perform other manufacturing steps.” But quietly, A123 has tackled these problems to become, as Fulop said, “one of the largest manufacturers of high-power lithium in the world, making them in the tens of millions.”
Discharge and Recharge
The company claims that its M1 batteries deliver more than 3 kW per kilogram and have ten times the cycle life of conventional lithium-ion batteries. And they’re not just in power tools. The A123 batteries are used now in auxiliary power units in aircraft, and earlier this year, General Motors selected the company’s battery technology to power a plug-in hybrid vehicle program it is developing with an eye to hitting the road by 2010.
For another new battery company, the big bet is on a market that has been tried many times before electric vehicles. Altair Nanotechnologies Inc., or Altairnano for short, of Reno, Nev., is in the process of delivering several dozen units of its 35 kWh Nanosafe battery to an upstart manufacturer, Phoenix Motorcars of Ontario, Calif. The plan is for Phoenix to have full-size, fully electric vehicles ready for shipment to fleet owners by the end of this year.
According to mechanical engineer Bob Goebel, who is Altairnano’s vice president of sales and marketing, the electrode in the company’s battery takes advantage of the nanoscale material. Conventional lithium-ion batteries have graphite electrodes, “and graphite is like a set of plates; as the charge changes, the plates shift,” Goebel said. “Also, the size of the lithium ion is larger than the gap between the graphite plates, so as you charge and discharge, you create a mechanical stress within the battery.”
Because the ions are larger than the gap, they can warp the shape of conventional graphite electrodes. Thanks to an advanced electrode made of nano-structured lithium titanate, the lithium ions in the electrolyte can migrate in and out of the electrode lattice without deforming it. That means the Altairnano battery can draw electricity quickly without overheating or causing damage to its internal structure and discharge steadily for a long time.
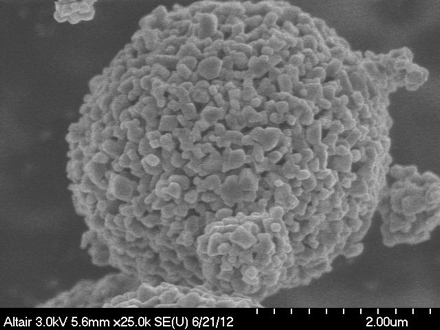
These claims, coming from a three-year-old start-up, were hard for some people to swallow. So the California Air Resources Board independently tested Altairnano’s battery packs. After subjecting the packs to three back-to-back 10-minute recharge/discharge cycles, the independent testers could find no sign of battery degradation and detected only a slight rise in temperature.
That sort of performance meets the specification for an electric vehicle, which needs to supply tens of kilowatts for two or three hours per charge, and then recharge rapidly. Such a vehicle, while maybe not ideal for long road trips, would more than suffice for daily travel.
But Goebel said that while the battery may be successful in the automotive realm, it is also well suited for stationary uses. The cost, however, is high now, about $2 a watt-hour. “We’ve got learning to do collectively, but we think we can shave the price in half pretty quickly. Once you can get the price below 50 cents a watt-hour, these batteries become attractive in tandem with renewable energy.” The scale is almost the same; he said: One battery pack stores nearly as much energy as the average household’s weekly electric consumption.
Although the A123 and Altair batteries have improved performance due to their incorporation of nanoscale materials, they store and release electricity through chemical reactions, the same as conventional batteries. But electricity can also be stored electrostatically—as ions clinging to a plate. First developed by Standard Oil in the 1960s, these so-called ultracapacitors are found in all sorts of electronic devices. They are efficient at storing and releasing electric charge, although historically they have not been able to hold energy as compactly as chemical batteries.
Better Than Sponges
That might change, thanks to research being conducted at a lab at the Massachusetts Institute of Technology. There, Joel Schindall and his colleagues are creating a new type of capacitor that, in theory, could not only be pound-for-pound as good at holding energy as a battery but could also have the advantage of being able to charge and discharge completely for a million cycles.
The key to boosting the charge density of an ultracapacitor is increasing the surface area onto which ions can glom. Many ultracapacitors presently use activated carbon, which has microscale pores. “This activated carbon has lots of imperfections, which limits the surface area,” Schindall said. “Other sites tend to be reactive with the electrolyte and break it down.” Because of these imperfections, the energy that can be stored is limited.
Schindall thought he could do better using material that was porous and uniform at the molecular level: an array of carbon nanotubes. Researchers have been making increasingly long nanotubes in the lab, including some that are a few tenths of millimeters long and just five nanometers thick. A carpet of nanotube filaments would have a surface area many times greater than a similar volume of activated carbon, and thus would be able to hold much more charge. “It’s like the difference between a paintbrush and a sponge,” Schindall said. “Sponges just don’t hold as much paint.”
But before nanotubes could form the heart of a new energy system, someone would have to figure out a new way to grow them. Conventionally, carbon nanotubes are grown like grass on a non-conducting silica substrate. Thus, any charge built up within the strands would have nowhere to flow. Schindall realized his team would need to find a way to grow the nanotubes on a metal plate if his capacitor idea was going to take off.

The first results have been quite promising: After some work, Schindall, along with colleagues John Kassakian and Riccardo Signorelli, demonstrated that nanotubes could rise from an aluminum electrode. By tweaking the way carbon is deposited on the electrode, his team was able to grow nanotubes within a few ion diameters from one another. Indeed, in some ways, the packed nanotubes resemble the molecular lattice found inside the lithium-ion battery, and simulations of the performance of a nanotube capacitor suggest it could pack in nearly as much energy in the same volume as today’s best batteries.
Schindall said the research had some way to go and that a marketable product wouldn’t be available this decade. But marrying the energy density of a battery with the durability and performance of a capacitor could eventually radically alter the way electricity is stored and used. Handheld devices could be recharged in seconds, not hours, and virtually all the remaining disadvantages of electric vehicles would melt away. What’s more, distributed electricity generation from home-based solar panels or combined heat and power systems could be backed up with a refrigerator-size capacitor unit that could store excess energy.
“In theory, you could recharge your laptop in just five or 10 seconds with one of these capacitors,” Schindall said. But he pointed out that to do that, you’d need to draw 200 amps, more than a home circuit could provide.
The promise of nanotechnology-enhanced energy storage is enough to make anyone see a limitless future. In some ways, this is little different than the type of enthusiasm that greets every nanoscale technology. And in that vein, A123’s Fulop cautions that nano-based storage systems ought to be looked at with optimism tempered by caution.
“For some of these far-out applications, you have to look 100 years down the road,” Fulop said. “With our technology, you’re talking about nanomaterials and microscale features within the battery pack. If you talk about storing gigawatt- or terawatt-hours, you have to apply those structures that are created with very high precision on a large scale. First, you have to crack the automotive mass market and build up the production base before we can even worry about the other stuff.”
[Adapted from “Nanoscale materials may soon revolutionize energy storage” by Jeffrey Winters, Associate Editor, Mechanical Engineering, August 2007.]